Projects
- Additive multi-material manufacturing (SAM) - This research project deals with the design of multi-material components for additive manufacturing, in particular laser powder bed fusion (LPBF). On the basis of practical test series, generally valid as well as machine- and material-specific recommendations for the additive manufacturing of multi-material components are to be formulated. The aim is to solve target conflicts through voxel-wise multi-material application and to produce shape-optimised components with locally adapted material properties.
- Design of particle-damped structural components - This research project is dedicated to the investigation of laser-melted particle dampers for vibration reduction. Experimental tests are being carried out to characterise the damping effect and a mechanical replacement model is being derived. The aim is to develop a verified mechanical replacement model for the highly non-linear relationships.
- Ellipse - Development methodology for laser-melted lightweight structures with integrated particle dampers for vibration reduction (DFG) - In this research project, which is being carried out in cooperation with the IDS of the LUH, multi-material particle dampers for vibration reduction are simulated, additively manufactured, characterised and validated on the demonstrator. The aim is a holistic physical evaluation of laser-melted particle dampers so that, based on this, a development environment with integrated multi-objective optimisation for the design of structural components with structurally integrated particle dampers can be developed in terms of stiffness, mass and damping.
- Innovative combustion systems through additive manufacturing (FVV) - The aim of the project is to optimise combustion in a high-load diesel piston by redesigning the bowl using additive manufacturing. The IPeG and its partners, the STFS at TU Darmstadt and the IFKM at KIT, are developing, manufacturing and testing the pistons. The focus of the IPeG is on the design of the thermal management and the production-orientated design and safeguarding of the component.
- Adaptation of a CHP unit using additively manufactured components for future hydrogen operation (NBank) - The IPeG is working with its partners ITV and ATRON GmbH on this project. Together, engine components are to be redesigned using additive manufacturing. The aim is to optimise the efficiency and increase the robustness of hydrogen engines for combined heat and power plants.
- RePare - Regeneration of product and production systems through additive repair and refurbishment (BMBF)- In this research project, strategies for the repair, modernisation and modification of metallic components using additive manufacturing processes are being investigated and implemented in practice. Recommendations for the design of repair process chains are being developed. Furthermore, tools are being developed to support designers in designing repair-orientated components. Further information can be found at: https://innovative-produktkreislaeufe.de/Projekte/RePARE.html
- Process-integrated lubrication in progressive drawing (EFB) - In this research project, which is being carried out in collaboration with the IFUM at LUH, a deep-drawing mould with integrated lubrication channels is being additively manufactured. The aim is to reduce lubricant consumption, lower tool costs and improve the surface quality of the drawn part. To achieve this, a lubricant cushion is to be created between the sheet metal and the tool surface by means of filigree oil outlet openings in the tool, which reduces friction and improves tribological conditions.
- Upscaling (Baker Hughes) - As part of the research project, a system model is being developed to merge data and models in various degrees of abstraction and maturity. To this end, various databases and formats at different levels of abstraction will be linked together in the system model, which will serve as input variables for multi-objective optimisation in order to improve the development of new deep drilling tools for various applications. The aim is to enable statements to be made about the condition of the components in deep hole drilling tools during use.
Expertise
- Design and simulation: Autodesk Inventor, Autodesk Netfabb Ultimate, Autodesk Netfabb Local Simulation, Abaqus, Ansys
- Development for additive manufacturing
- Experimental investigations
Equipment
- Additive learning factory
- System for laser powder bed fusion
- System for the production of multi-materials in laser powder bed fusion
- Installation space-independent system for laser powder bed fusion
- Process monitoring
- Micro-computer tomograph
- Surface measurement fringe projection
- Multi-physics test bench
- Vibration measurement technology
- Oven for heat treatment
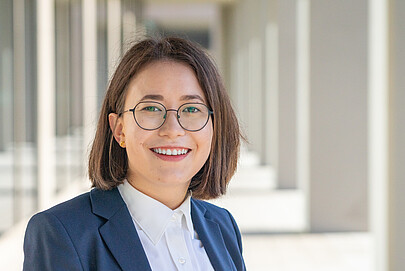
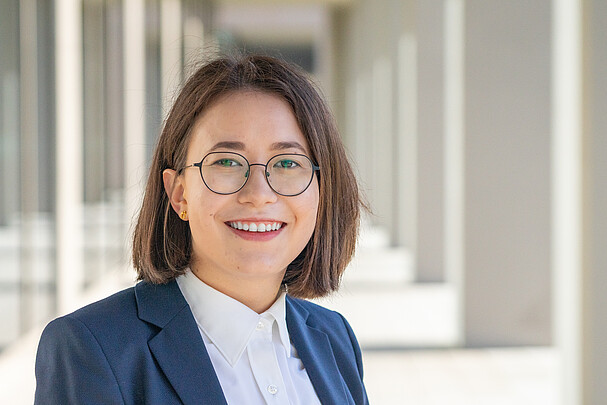
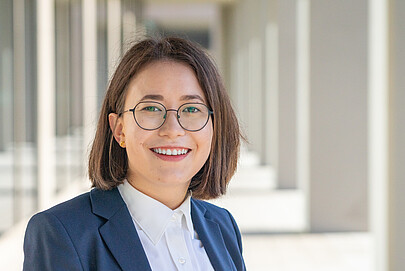
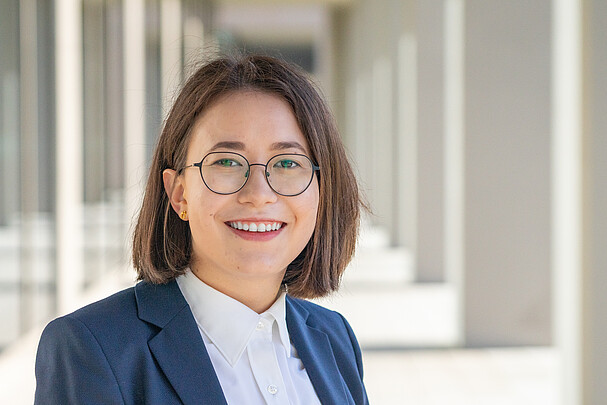